Maintain Your Moving Parts
Just because the wheels are turning doesn't mean they're going forward.
Get your motor runnin'
"Just a typical day at our 50-year-old pharmaceutical factory," sighs our GMP Agent-in-Place. "A mixing motor for a vessel burned out, and a replacement was ordered from the original equipment manufacturer. An identical model was ordered, received, installed, and put to use. You have to understand that the mixer (motor) was used at full speed; there was no variable-speed control, just 'ON' and 'OFF.'
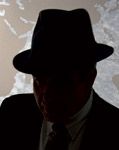
Control
"After several batches, the production manager noted that not only was there more variability in product potency, but worse, there also was a yield decrease that would affect his bonus, and he didn't know why. After an extensive investigation, it was determined that the replacement motor was geared to 1750 rpm, rather than the 3000 rpm of the original, even if it was the correct model number. With slower mixing, there was insufficient reaction to give full yield. Of course, the motor was replaced as soon as possible after the reduced rpm factor was discovered, and the specifications were changed to clearly specify rpm."
Having a ball
"A 50-year-old tablet-product ingredient needed to be milled finely to achieve proper color and particle size, and a ball mill was used," explains our GMP Agent-in-Place.
(For those of you who don't remember ball mills, they are uncommon [i.e., never found] in the pharmaceutical industry. A ball mill is a large cylinder with cleats attached around the inner circumference and is filled approximately half-way with steel balls. During the mill's very noisy rotation, the balls fall repeatedly onto the product, mashing it fine.)
"We shipped the finished material to our sister company for use in tablet manufacture. They started complaining about the rust and iron particles in the product. It turned out that neither the balls nor the cleats were stainless steel and were rusting. Of course, the vigorous pounding in the ball mill ensured the particles would flake off into the product. The fact that most particles were tiny and no danger to anyone didn't make us feel any better, because some balls were literally falling apart, and larger pieces of metal were ending up in the milled ingredient. So I rejected many batches over the objections of the production manager who had been running this equipment for decades.
"Although the short-term fix was to purchase stainless steel balls as a replacement, we realized that even with decades of experience, the ball mill was not a pharmaceutical piece of equipment. It was prone to emitting iron particulates, and couldn't be cleaned effectively. A cleanable 'pharmaceutical-grade' mill was finally purchased and put into service."
All pumped up
"The pump broke and was repaired, and it wasn't my fault," grouses our GMP Agent-in-Place. "You see, lyophilizers (freeze dryers) require pumps to remove air and to circulate coolant through the shelves. In this case, repairs were made, and the pump reassembled. It was tested off-line and rotated well, so it was put into use.
"But, our mechanic assembled the pump with the impeller backwards, the pump didn't work and so the batch in the lyophilizer at the time was ultimately rejected."
Pharmaceutical Technology's monthly "Agent-in-Place" column distills true-life cautionary tales from the secret files of Control, a senior compliance officer. If you have a story of clueless operators, oblivious management, inopportune lapses of judgment, or Murphy's Law in action, please send it to Control at AgentinPlace@advanstar.com. We won't use any names, but if we do use your tale of disaster, courage, or just plain weirdness, Control will send you a coveted Pharmaceutical Technology t-shirt.
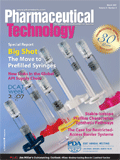